SMC and BMC in the automotive industry
Composites are used in automotive and truck industry for over 50 years now.
Major reasons for automotive are weight reduction and design freedom as also cost competitiveness. SMC and BMC are widely used for exterior body panels. SMC and BMC are the best solution for weight reduction on a vehicle while stiffness or temperature performance or on-line paintability are basic demands and are also provided.
Examples are the decklids of various Coupés and Cabrioléts such as Renault Megane Coupe and Cabriolét, Ford Thunderbird and Volkswagen EOS.
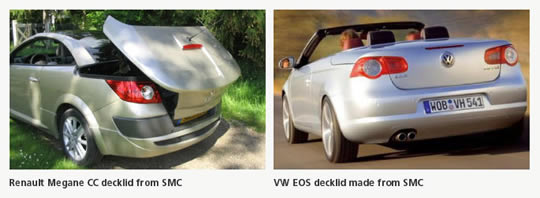
The Thunderbird also has SMC fenders, hood and a tonneau cover made from SMC.
Since car bodies made of SMC / BMC have been realised (examples Chevrolet Corvette & Camaro, Renault Espace, Pontiac Fiero, GM Lumina APV and DC Viper, Renault Avantime, VOLVO ES 480) we can see structural components made of SMC coming up soon using the potential for more weight reduction.
In a project run by Menzolit and VW it was clearly demonstrated that an inner structure/ frame of a vehicle is feasable and can fulfil all requirements regarding stiffness and crash worthiness. A quarter body section with A and B pilar was made out of high performance compound (Menzolit-HPC) and moulded as two parts which were bond together with adhesive.
Newly designed Menzolit SMC 1800 is specialised to serve structural applications.
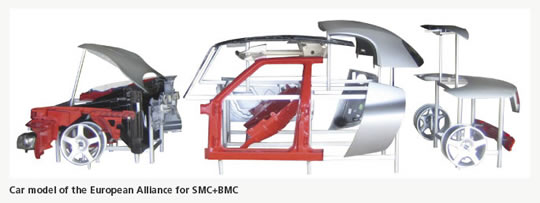
In the engine compartment SMC and BMC are used for oil sumps, valve covers and more and more for smaller precision devices such as throttle bodies and inlets.
Menzolit has specially designed materials for this use:
Menzolit SMC 1400
Menzolit BMC 1400
Lighting systems become very hot especially those which are encapsulated with a Polycarbonate window instead of glass.
Therefore many headlamp reflectors world wide are injection moulded from BMC. Menzolit offers special grades of SMC and BMC:
Menzolit BMC 3100
Features, Advantages and Benefits of SMC / BMC parts:
- Perfect surface
- On-line, in-line and off-line paintable
- Parts integration
- Light weight
- Low system cost
- Integration of functions
- Easy to bond
- Stiff
- Good mouldability
- Complex shape
- Weathering resistance
- Low moulding pressure
- Low tooling cost
- No corrosion
- High stiffness & strength
Cost comparison of SMC versus sheet metal
Nowadays, car manufactures diversify their product portfolio significantly. Using the same platform with different body work leads often to annual number of vehicles between 30.000 and 100.000. Here MenzolitSMC offers not only weight savings but also – and that is even more important – a cost advantage.
Following we are showing a cost comparison of a tailgate made of Steel vs. SMC.
The tailgate is made from an inner support and an outer skin which are bond together and then painted. If the tailgate is made from sheet metal the aprts are welded sealed and corrosion protected before painting. To form these parts from metal 5 to 6 tools for the outer skin and further five for the inner shell are necessary. For SMC only one tool needed for inner and outer part for volumes up to 60.000 and 2 of each for twice the volume. Exceeding these numbers up to 80/160.000 an additional tool per shell is advised to have delivery security. With high volumes sheet metal is definite the more inexpensive alternative.
Cost comparison of tailgates made from sheet metal versus SMC
End of life of vehicle
The ELV regulation of the EU requires a detailed evaluation of parts used on the vehicle regarding ecological behaviour and recyclability.
Therefore a decklid concept was evaluated under the parameters of an eco balance and three models were compared to each other: aluminium, sheet metal and SMC.
SMC shows the best eco-efficiency.